|
|
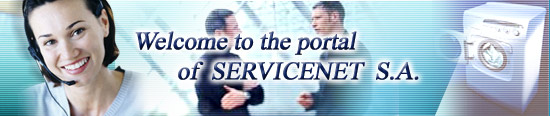 | 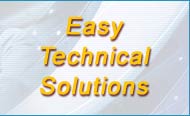 |
|

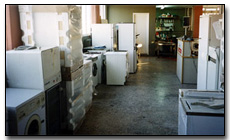
Our laboratory has vast and modern spaces, which were designed so as to combine comfort and functionality. It is divided in three halls, the first of which shelters the main service hall, equipped with all the hi-tech tools, required for the repair of all appliances. The second one is storage for massive arrivals of appliances and the last one is a laboratory for the repair of small appliances such as irons, vacuum cleaners and microwave ovens. Our aim is to repair all the appliances as soon as possible, offering the highest quality of service.
For the operating center of our company, we have been supplied with a hi-tech telephone device, with 22 lines, for the immediate respond to our customers and colleagues. Our technicians' hall is connected to the operating center in order to achieve an immediate communication between the administration and the final consumer. This center has given us the opportunity to create a sub-center destined exclusively to the warehouse so as to ease the company's main operating center and to accelerate our customer's access to the warehouse.
Furthermore, a specialized counting system allows us to maintain a full file and data concerning every single call. ( ISDN lines-calls' verification-numbers dialed by every extension-calls' duration-charges etc.). These data that we gain on daily basis, demonstrate that the average conversation with the customer lasts for 2'30". This time space includes the introductory message for every company, the hold until the call is taken and the conversation with the staff of the operating center. Of course all these data are available at any time, after prior request.
Based on a research of the public relations' domain of the company concerning our efficiency in the field by companies relative to service, we are in the pleasant position to inform you that our efficiency is absolutely perfect.
Moreover, our company, in the attempt to supervise the efficiency of the external staff and of the transporters has installed in everyone of our vehicles a chip, which has the possibility to be connected to the brain of every vehicle, in order to record every movement of the vehicle. This chip is connected to the main computer of the company and gives us the possibility to check the vehicle's movement, on any day and at any time we wish. This system records the kilometric distance between places, the time required, the time that the technician used to repair the malfunction for which he was called, the highest speed at which the vehicle run, the time of departure from the company, as well as the time that the technician completed his schedule.
Combining all these elements, the chip is scheduled and suggests the amount of overtime for every driver, and based on factors created by the company, supervises his efficiency. Certainly, all these data are available to print.
Additionally, we present you the vehicles of our company, which include 2 vans fully equipped to facilitate transports, 1 for the transport of packages and 8 for the needs of the exterior service. All vehicles use unleaded fuel and therefore are friendly for the environment. Besides, all vehicles cannot electronically overcome the limit of 80 Km/h in the city, so as to protect the driver. Every vehicle includes a mini warehouse that contains spare parts for common malfunctions in order to offer a better and more immediate service to the final consumer, diminishing at the same time useless transfers and waste of valuable time.
|
|
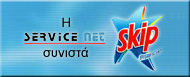
|
|
|
© 2005 Designed & Hosted by Microquest |
|